Our unyielding commitment to innovation and continuous improvement has enabled us to remain at the forefront of technological advancement, ensuring that our customers receive the best solutions needed for revolutionizing aluminum production. As most of our R&D work focuses on recycling technology, our fundamental goal is to make the aluminum industry eco-friendlier.
Established in 2016, ST R&D Center today houses a team of 60 engineers and designers who work on the goal of delivering smart factories that can work independently of human interactions and interventions. We believe foundries must become a more manageable place by developing safer, faster, and more efficient systems. In addition, our studies on artificial intelligence applications have been guiding the development of new ST products since 2019.

At Sistem Teknik, we put sustainability at the center of our strategic decisions. In the past 5 years, Sistem Teknik has dedicated 85% of its R&D budget to reducing emissions in aluminum production, with efforts culminating in the development of 5 new equipment for the aluminum melting and heat treatment processes. These products include delacquering drum furnaces, preheating ovens targeting heat recuperation, camera integration systems for efficiency predictions, ultra-low NOx burners, and fully automated charging and skimming mechanisms in cast houses that shorten melting cycles.
In 2020 our R&D center was awarded a partnership in the Horizon Europe platform for its commitment to developing greener ways of recycling and processing aluminum and was funded by the European Commission. In line with the projects’s requirements, we delivered various equipment at the demo-site, ASAŞ Aluminium. This project was only the first step in our path to being able to deliver cast houses and heat treatment plants with zero emissions.
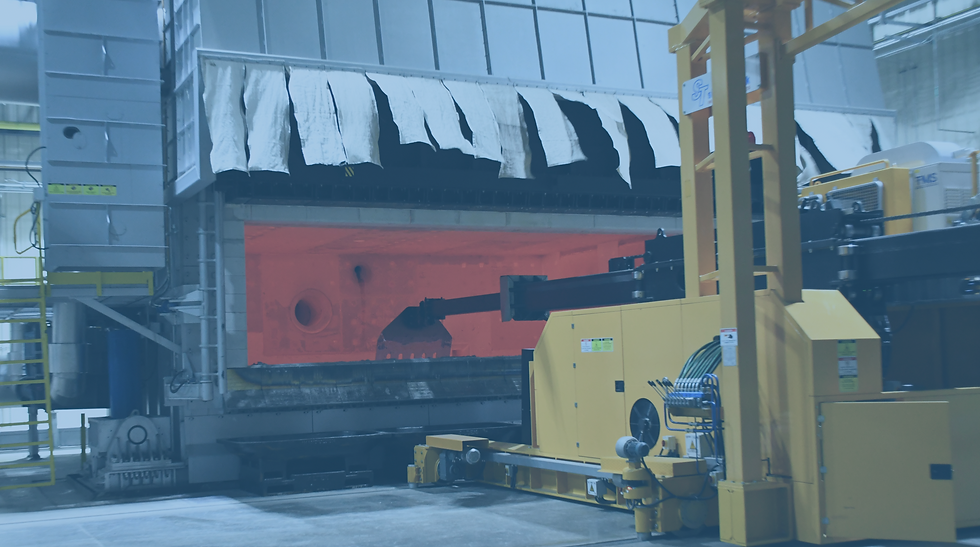
Sistem Teknik R&D center recently developed a fully-automated skimming machine that utilizes image processing to detect dross formation. Now, it is one of the most sought-after equipment we offer to aluminum producers.
New models developed in our R&D center are protected through frequent patent applications (an average of 10 patent applications per year) and utility model certifications, reflecting the importance we place on intellectual property rights. For its R&D activities, our company has received numerous awards.
In addition to our long history of being a forerunner of innovation in the aluminum sector, our company has gained sector-specific applications in autoclave designs used by brands such as Airbus, Boeing, Sikorsky, and the Turkish Aviation Industry (TUSAŞ) in the last decade. Sistem Teknik’s patented carbon fibre composite autoclave design was awarded by Turkey’s Scientific and Technological Research Council (TÜBİTAK) in 2013.
Currently, Sistem Teknik focuses on academic partnerships and collaborates with many professors and researchers mainly in the field of metallurgical engineering and physics.

.png)
What Does STAR Lab Do?
Advanced research plays a crucial role in driving innovation and shaping the future of industries. New technologies, materials, and processes can only be developed when know-how meets cutting edge research. In 2022, we have founded the Sistem Teknik Advanced Research (STAR) laboratory with this awareness. Along with our Prototype Testing Laboratory, the STAR Lab serves an important purpose for conducting basic R&D studies on optical laser spectroscopy technologies. We have collaborated with universities and R&D companies to gain knowledge on fields that are new to the Sistem Teknik R&D Center and develop pioneering solutions for the aluminum industry. Through this strategic decision, we will be able to increase the technological readiness of industrial furnaces for full automation and zero emissions production.
New Projects
-
The STAR Lab is currently conducting an R&D project on elemental analysis of molten metal using Laser-Induced Breakdown Spectroscopy (LIBS) technology, which is being funded by TÜBİTAK. The knowledge gained from this project will be used to support the development of LIBS technology for aluminum recycling within the framework of the EUROSTARS program, with the ultimate goal of integrating this technology into ST's industrial furnaces and commercializing it.
-
The STAR Lab will conduct studies aimed at developing the nanosecond pulse laser and high-resolution spectrometer necessary for Laser-Induced Breakdown Spectroscopy (LIBS).
-
The development of a system that will be able to sort faster by using 4 different channels on the conveyor belt is among the primary objectives of the STAR Lab.
-
Laser-based thin film coating technologies on aluminum decking materials are also another research subject that the STAR Lab is currently working on.
-
We are also developing technologies for producing aluminum materials at the nanoscale. Our goals include using nano-sized aluminum in hydrogen energy production, rocket fuel technologies, and optical thin film coating (such as PLD - Pulsed Laser Deposition).
Why LIBS?
We consider LIBS to be imperative for the future of the aluminum industry as it shortens casting cycles by up to 40 minutes, significantly reducing the emission of greenhouse gases and energy consumption since the analysis takes place when the metal is in liquid form.
With the development of LIBS technology, we provide aluminum producers with the option of determining the in-situ chemical composition during the melting process. Sample collection for elemental analysis is made by fully automated systems with a no-man- on-the-ground perspective to ensure operational health and safety.

How does it work?
-
The probe is immersed to the required depth in molten metal
-
The probe is filled with pressurized argon gas to prevent liquid metal to fill the probe
-
The laser is propogated through the probe and focused onto the liquid metal
-
A spectrometer is used to measure the emission that occurs in a liquid metal
-
According to this measurement, the elements’ proportions are measured
-
After the measurement, missing elements are detected with regards to the prescription
+90 262 658 22 26
+359 89 295 6561
LEARN ABOUT OUR